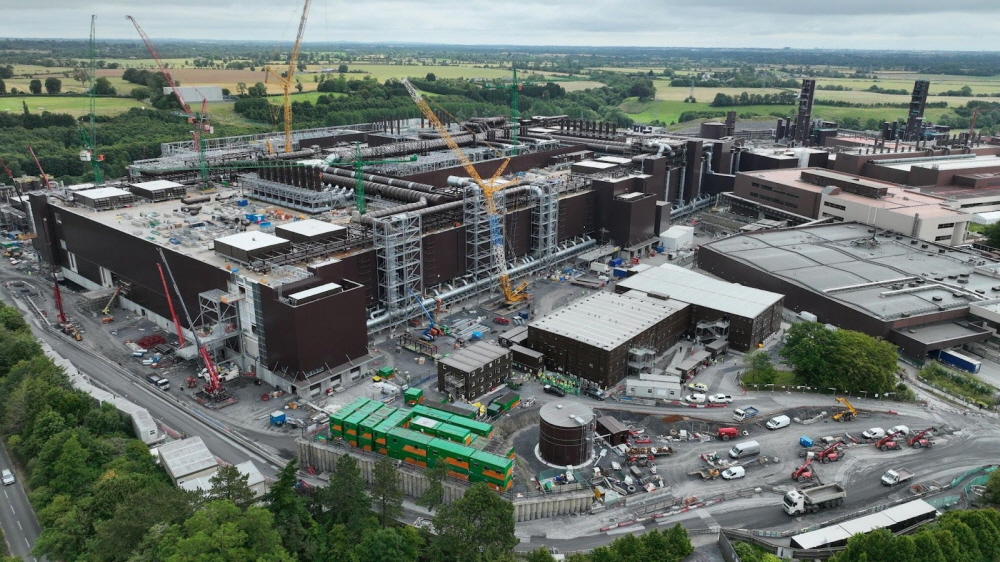
반도체는 전도율을 수십억 배까지 변화시켜 전자 흐름을 차단하거나 허용할 수 있는 재료로 PC를 비롯한 모든 전자기기에 필수적이다. 수십 년간 기술 발전으로 반도체 비용과 크기는 낮아졌지만 역설적이게도 반도체 제조 공장 비용은 수조 원 수준까지 치솟았다.
1970년대 반도체 공장 평균 건설비용은 310만 달러였지만 2020년경에는 200억 달러 규모 공장이 차례로 건설되기 시작했다.
이렇게 건설비용이 상승한 이유는 반도체 제조 공정 때문. 컴퓨터 칩 단면을 보면 여러 층으로 이뤄진 복잡한 구조다. 하단 FEOL로 표시된 영역에 트랜지스터 등 반도체 주요 부품이 설치되고 상단 BEOL 층에 다수 부품들이 상호 연결된다. 사용되는 트랜지스터 수가 증가할수록 배선이 복잡해지며 10층 이상의 BEOL 층이 있는 건 드문 일이 아니다.
칩은 이런 복잡한 구조를 한 층씩 쌓아 올려 만들어진다. 칩 구조를 구축할 때는 레이어링, 패터닝, 도핑, 열처리 등 4가지 작업을 거친다.
먼저 레이어링. 머리카락 지름 10만분의 1에 불과한 1나노미터 두께 층을 웨이퍼 표면에 추가한다. 기술이 발전함에 따라 적층 공정에도 높은 정밀도가 요구되어 최신 원자층 증착법으로는 단일 원자층을 만들 수 있게 됐다.
이어 패터닝. 웨이퍼 위에 특정 패턴을 새기고 필요에 따라 재료를 선택적으로 제거한다. 현대에는 포토리소그래피가 사용되며 감광성 재료를 코팅한 뒤 패턴이 새겨진 마스크판을 통해 빛을 비춰 화학반응으로 패턴을 인쇄한다.
다음으로 도핑. 반도체 재료에 극소량 불순물을 도입해 전도율을 변화시킨다. 불순물 종류에 따라 자유전자가 과잉인 n형 반도체와 정공이 과잉인 p형 반도체가 생성되며 이를 적절히 배치해 트랜지스터를 만든다. 과거에는 기체 원자를 웨이퍼에 반응시켜 도핑을 했지만 현재는 이온빔을 조사하는 방식을 이용한다.
마지막으로 열처리. 이온빔 조사로 실리콘 결정 구조가 손상되므로 수초 만에 1,000도까지 웨이퍼를 가열한 뒤 천천히 냉각시켜 결정 구조를 복구한다.
이 4가지 기본 공정 외에도 연마, 세정 등 다수 보조 공정이 있다. 화학기계연마(CMP)로 웨이퍼 표면을 매끄럽게 하고 에칭으로 생긴 구멍을 메운다. 세정 공정에서는 용액과 순수로 웨이퍼를 계속 씻어 미세 부유 입자를 제거한다. 대부분 공정은 부유 입자를 최소화한 클린룸에서 이뤄지며 여러 지점에서 웨이퍼를 측정해 결함 유무를 확인한다.
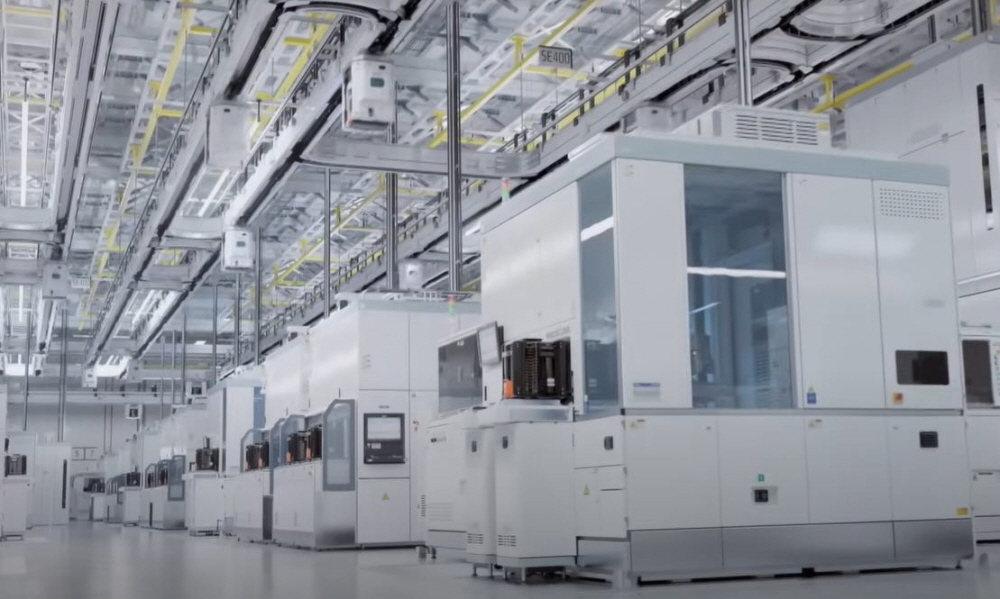
이렇게 4가지 주요 공정과 다수 보조 공정을 반복적으로 적용해 반도체 구조를 천천히 구축해 나간다. 현대 제조 공정에서는 80매 이상 마스크와 수천 번에 이르는 공정 단계가 필요하다.
회로 구조가 완성되면 조립 및 패키징 공정으로 넘어간다. 웨이퍼를 개별 칩으로 분리한 뒤 각 칩을 와이어에 연결하고 보호 코팅한다.
반도체는 공정 단계가 많은 복잡한 제품일 뿐 아니라 크기도 매우 작아 극도로 정밀도가 요구된다. 일반 제조 공정에서는 0.05mm~0.2mm 정도 오차가 허용되지만 반도체의 경우 공정 게이트 간격이 0.000051mm 그러니까 51nm에 불과하다. 한 입자가 섞여 회로를 단락시키면 칩 전체가 작동하지 않게 된다.
반도체 제조 역사는 작은 요인으로 인한 파괴적 영향과의 전투 기록이라고 할 수 있다. 1940년대 벨연구소에서 반도체를 연구할 때 원인을 알 수 없는 부품 고장이 발생했는데 이유는 연구원이 구리 문고리를 만져 손에 극미량 구리 원자가 묻어서였다. 초기 반도체 제조업체는 수율이 월명, 직원 화장실 이용 시간, 여성 직원 생리 주기에 따라 달라지는 걸 발견했다.
반도체 기술이 발전하면서 제조 시 요구되는 청결도 수준도 높아졌다. 현대 반도체 공장은 청결한 환경 조성을 위해 4개 계층을 갖추고 있다. 가장 위에는 팬과 필터가 설치되어 있어 2계층 클린룸 공기 순환을 돕는다. 클린룸 아래에는 2개 계층 지원용 층이 있어 클린룸 설비 배관, 배선, 장비가 설치되어 있다.
클린룸 안에는 리소그래피 장비, 화학증착기, 이온주입기, 웨트벤치 등 다양한 반도체 제조 장비가 있다. 장비는 종류별로 모아 배치해 각 공정에서 사용되는 화학물질을 격리시킨다. 또 기둥과 벽 영향을 최소화하기 위해 지붕을 크고 긴 트러스 구조로 해 클린룸 공간을 최대한 열어뒀다.
일반 주택에는 공기 1입방피트당 0.5μm 이상 입자가 50만 개 정도 있고 수술실에도 10만 개가 떠다니지만 반도체 공장 클린룸에서는 클래스별로 0.5μm 이상 입자가 10∼100개 이하로 관리된다. 입자 유입을 막기 위해 클린룸은 외부에 대해 정압을 유지하고 1시간에 510회 환기가 이뤄진다.
웨이퍼에 직접 닿는 공기는 0.5μm 이상 입자가 0.1개 이하여야 하므로 제조사는 클린룸 안에 미니 클린룸을 만들어 웨이퍼를 처리한다. 장비간 웨이퍼 이동에는 밀폐된 FOUP 포드가 사용된다.
현대 공장에서 FOUP는 천장 레일시스템을 따라 움직인다. 복잡한 제조 공정 때문에 웨이퍼가 공장을 지나는 데 수개월이 걸리며 항상 웨이퍼 수만 장이 공장 안에 있다. 이렇게 많은 웨이퍼를 처리하려면 수km 궤도와 이송 차량 수천 대가 있는 원활한 교통 시스템이 필요하다.
제조 공정에 영향을 주는 건 부유 입자 뿐만이 아니다. 반도체 공장은 진동에도 민감해서 과거에는 공장에서 100m 떨어진 배기구가 클린룸 바닥에 허용 수준을 벗어나는 진동을 일으켰던 적이 있다. 공장은 일반 건물 100배에 이르는 기계 에너지와 50배 공기 흐름을 흡수하고 진동을 인간 지각 한계치보다 수 단계 낮춰야 한다.
진동을 최소화하기 위해 클린룸 바닥은 1m 가량 두꺼운 콘크리트 와플 슬래브 구조로 지었고 조밀하게 배치된 기둥으로 견고하게 받쳐 있다. 슬래브 위에는 금속 바닥을 설치해 제조 기기를 사람 동선과 분리했다. 리소그래피 장비 등 까다로운 진동 요건이 있는 기기에는 진동 감지‧상쇄 장치가 필요하다. 경우에 따라서는 클린룸 바닥을 건물 다른 부분과 물리적으로 분리하기도 한다.
클린룸 건설에다 배관, 약품 보관 등을 합치면 넓은 부지와 다량의 자재, 특수 공법이 필요해 비용이 많이 드는 건 당연하다. 하지만 현대 반도체 공장에선 건설비보다 생산 장비 비용이 더 비싸다. 1980년대에는 건설비와 장비비가 반반이었지만 1990년대 후반부터는 장비비가 대부분을 차지하게 됐다.
그중에서도 리소그래피 장비 비용이 가장 높아 공장 건설비와 맞먹을 정도다. 그 다음으로 증착, 세정, 에칭 장비 비용이 높다.
반도체 제조 기술이 발전하고 트랜지스터가 작아질수록 공장 비용도 올라간다. 공정 노드가 하나 발전할 때마다 장비비가 많이 들고 층수가 늘어 공정 단계 수도 늘어나 제조 비용이 30% 증가한다.
이렇게 공장 비용이 오르면서 반도체 산업 구조도 바뀌었다. 공장이 싼 시절에는 어느 칩 업체나 공장을 지을 수 있었지만 비용이 올라가자 규모의 경제를 실현할 생산량을 갖춘 업체만이 최신 공장을 건설할 수 있게 됐다. 예를 들어 150mm 웨이퍼 공장의 경우 월 1만 장 생산이면 효율적이지만 300mm 로직 웨이퍼 공장은 최고 효율을 내려면 월 4만 장을 생산해야 한다.
따라서 최첨단 반도체 제조는 TSMC, 삼성전자, 인텔 등 몇몇 업체만 하게 됐고 애플, 엔비디아 등은 칩 설계만 하고 TSMC 같은 파운드리에 제조를 맡기게 됐다. 파운드리 업체는 여러 칩 업체 주문을 받아 최신 대형 공장을 효율적으로 가동할 수 있게 된 것이다.
이렇게 반도체 공장 규모가 거대해지고 그 안에서 24시간 365일 원자 수준 작업을 지속해야 하는 요인 때문에 공장 건설비용이 천문학적인 수준이 된 것이다. 관련 내용은 이곳에서 확인할 수 있다.