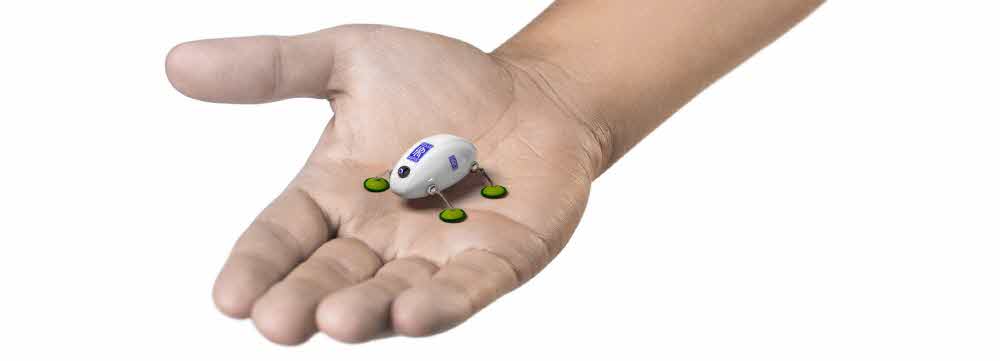
롤스로이스홀딩스(Rolls-Royce Holdings)가 비행기 엔진 내부에 들어가서 마치 바퀴벌레처럼 엔진 상태를 검사할 수 있는 초소형 로봇을 개발한다고 발표했다.
이 같은 구상은 롤스로이스홀딩스가 지능형 엔진 비전을 발표하면서 밝힌 것이다. 지능형 엔진은 데이터 수집과 인공지능 기술을 접목해 서비스 관리에 특화한 항공기 엔진 개발을 목표로 한 것이다. 롤스로이스홀딩스 측은 엔진 자체의 유지 보수나 적응성을 높이기 위해 기체 엔진과 제어 장치, 지상 고객과 정비사간 실시간 정보 공유, 엔진 관련 상황을 자동 인식해 인간의 개입을 기다리지 않고 자동 적응, 축적한 기록이나 네트워크상 다른 기체 엔진 기록 등을 참고해 최적의 성능을 내는 걸 말한다고 설명한다.
이런 일환으로 개발된 게 바로 벌레 로봇(SWARM robots)이다. 하버드대학 연구팀과 공동 개발하는 이 로봇은 엔지니어가 비행기 엔진을 굳이 분리하지 않아도 내부 모니터링을 할 수 있도록 해주기 때문에 유지 보수성을 크게 높일 수 있다는 장점을 기대할 수 있다.
비행기에 들어가는 엔진은 복잡한 구조로 이뤄져 있는 탓에 유지 보수에도 상당 시간이 필요하다. 유지보수용 소형 로봇은 엔진 외벽에 만든 작은 구멍을 입구로 이용한다. 구멍에 붙은 작은 덮개를 빼고 얇은 튜브를 넣는다. 엔진 깊숙한 곳까지 들어간 튜브를 통해 검사 지점까지 도달하게 된다. 이렇게 하면 튜브 끝에서 소형 로봇이 나온다.
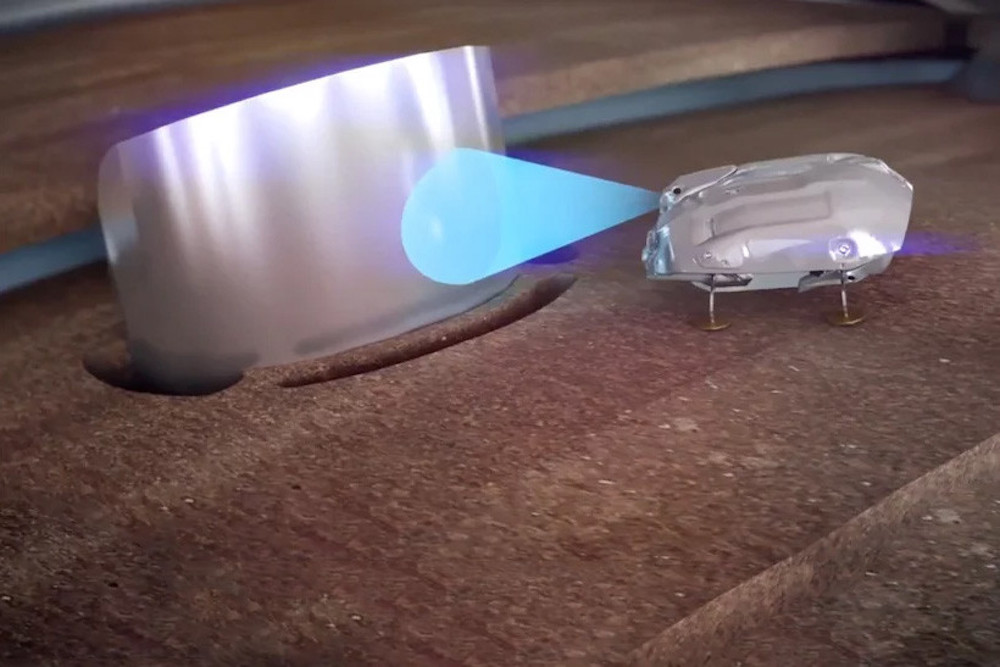
소형 로봇은 작고 얇은 다리를 갖춰 마치 이동속도가 느린 바퀴벌레처럼 벽을 기어 올라가거나 내려간다. 로봇에 장착한 소형 카메라를 이용해 내부 상황을 모니터링하고 문제가 없는지 꼼꼼하게 체크한다. 소형 로봇은 한꺼번에 여러 대를 투입해 각자 맡은 검사 범위를 분담, 효율적으로 검사할 수 있다. 당연히 검사한 장면은 원격으로 확인할 수 있다. 엔지니어는 이를 통해 엔진 내부에 들어갈 필요 없이 확인할 수 있다.
모든 검사가 끝나면 소형 로봇은 다시 알아서 튜브로 돌아온다. 로봇을 모두 회수한 다음 튜브를 당기면 끝. 복잡한 엔진도 안전하고 쉽게 검사할 수 있다.
항공 분야에서 IT 기술을 접목하려는 시도는 꾸준히 이뤄지고 있다. 롤스로이스홀딩스와 프랫앤휘트니와 더불어 세계 3대 제트엔진 제조사로 꼽히는 GE 역시 지난해 3D프린터를 활용해 항공기용 제트엔진 부품을 생산하는 3D프린터 개발 소식을 발표하기도 했다. GE 산하 GE애디티브(GE Additive)가 지난해 파리에어쇼 당시 발표한 것.
이 3D프린터는 소재인 금속 분말을 얇은 층으로 쌓은 다음 레이저를 조사해 굳히는 금속 가공 기술(Additive GE Manufacturing)을 이용했다.
쉽게 말하자면 금속 가루를 쌓아서 굳히고 싶은 부분에 레이저 빛을 쏜다는 것이다. 높은 에너지를 지닌 레이저 빛을 받은 부분에만 불꽃이 올라오면서 순식간에 용해가 되고 이 과정을 거치면서 금속 부품이 만들어진다. 용접이나 절단 같은 작업 없이 바닥에 위치한 토대를 바꿔가면서 금속 가루를 조금씩 바꿔가며 쌓아 형태를 바꿔 입체적인 부품을 만든다.
이 기술은 기존과는 비교할 수 없을 만큼 높은 자유도로 금속 가공을 할 수 있다. 항공기 부품이 요구하는 강도나 가벼움은 물론 안정성을 균형감 있게 구현할 수 있다는 것이다. 3D프린터를 이용한 방식의 장점은 컴퓨터로 만든 데이터와 3D프린터만 있다면 복잡한 형상도 언제 어디서나 만들 수 있다는 것이다. 또 기존에는 금속 가공이라고 하면 성형과 절단, 접합이 주였지만 금속 소재를 녹이면서 쌓아서 붙이는 새로운 가공 방식이 등장했다는 것도 눈에 띈다. 3D프린터로 금속을 가공해 지금까지 어렵던 금속 부품 구조를 간단하게 구현할 수 있게 해줄 수 있다는 것이다.
GE는 이미 3D프린터로 만든 연료 노즐을 채택한 엔진인 리프(LEAP)를 선보인 바 있다. 주로 소형 항공기를 위한 것이었다면 위에서 설명한 엔진은 가로세로 크기가 1m에 이른다. 대형 제트엔진 부품 생산도 가능한 크기다. 이렇듯 항공 분야에서도 IT와 접목해 혁신을 추구하려는 노력이 계속되고 있다.